Choosing the right Plastic Injection Molding Machine is crucial for any manufacturing process. The correct machine ensures high-quality production and minimizes operational costs. Cost considerations play a significant role, with plastic resins ranging from $0.90 to over $2 per pound and injection molding costs varying widely based on order size and part complexity. The selection process involves evaluating factors like production efficiency, energy consumption, and product quality. Balancing affordability with functionality is essential for making an informed decision.
Understanding Plastic Injection Molding Machines
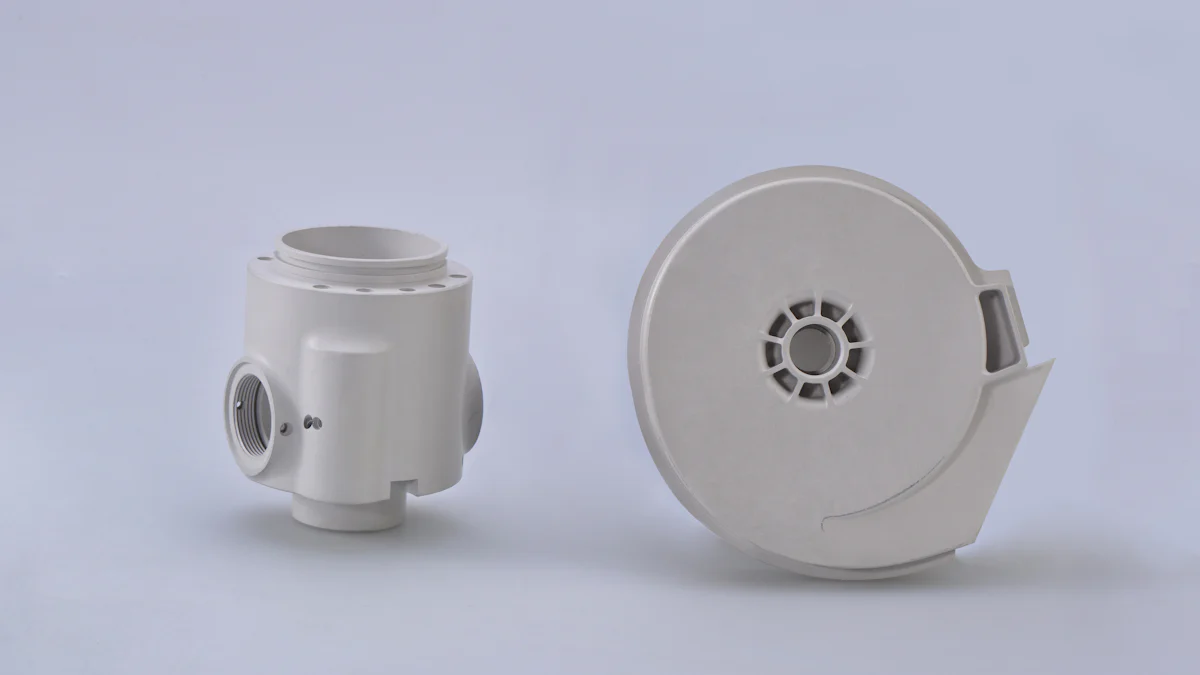
Basic Components
Injection Unit
The injection unit plays a crucial role in the Plastic Injection Molding Machine. This unit melts the plastic resin and injects it into the mold. The injection unit consists of a hopper, barrel, and screw. The hopper feeds plastic pellets into the barrel. The barrel heats the pellets until they melt. The screw pushes the molten plastic into the mold cavity.
Clamping Unit
The clamping unit holds the mold in place during the injection process. This unit ensures that the mold remains closed under high pressure. The clamping unit consists of a fixed platen, moving platen, and tie bars. The fixed platen holds one half of the mold. The moving platen holds the other half and moves to open and close the mold. The tie bars provide structural support to keep the platens aligned.
Control System
The control system manages the entire operation of the Plastic Injection Molding Machine. This system includes a user interface, sensors, and software. The user interface allows operators to set parameters such as temperature, pressure, and cycle time. Sensors monitor these parameters and provide real-time feedback. The software processes this data to ensure optimal machine performance.
Types of Plastic Injection Molding Machines
Hydraulic
Hydraulic machines use hydraulic cylinders to generate the force required for the injection and clamping processes. These machines offer high power and are suitable for producing large parts. Hydraulic machines are generally more affordable but consume more energy compared to other types.
Electric
Electric machines use electric motors for all movements, including injection and clamping. These machines offer high precision and energy efficiency. Electric machines are ideal for producing small, intricate parts with tight tolerances. Although the initial cost is higher, the operational savings make them cost-effective in the long run.
Hybrid
Hybrid machines combine the best features of hydraulic and electric machines. These machines use electric motors for precise movements and hydraulic cylinders for high-force applications. Hybrid machines offer a balance between power and efficiency. They are versatile and can handle a wide range of production requirements.
Key Factors to Consider
Budget Constraints
Initial Cost
The initial cost of a Plastic Injection Molding Machine can vary significantly. Factors influencing this cost include machine type, size, and features. Hydraulic machines generally have a lower initial cost compared to electric or hybrid machines. However, the choice should align with production needs and long-term goals.
Operating Costs
Operating costs also play a crucial role in the decision-making process. These costs encompass energy consumption, maintenance, and labor. Electric machines offer higher energy efficiency, reducing long-term operating expenses. Maintenance requirements differ among machine types. Hydraulic machines often need more frequent servicing. Labor costs depend on the complexity of the machine’s operation and the level of automation.
Machine Specifications
Tonnage
Tonnage refers to the clamping force of a Plastic Injection Molding Machine. This force keeps the mold closed during injection. The required tonnage depends on the size and complexity of the part being produced. Larger parts or those with intricate details may require higher tonnage. Proper calculation ensures optimal performance and prevents defects.
Shot Size
Shot size indicates the amount of plastic injected into the mold in one cycle. The shot size must match the volume required for the part. An oversized shot size can lead to material waste. An undersized shot size may result in incomplete parts. Selecting the appropriate shot size is essential for efficient production.
Mold Size
Mold size compatibility with the Plastic Injection Molding Machine is vital. The mold must fit within the machine’s platen dimensions. Incompatible mold sizes can cause operational issues and affect product quality. Ensuring mold size alignment with machine specifications enhances production efficiency.
Manufacturer Reputation
Brand Reliability
Brand reliability impacts the long-term success of using a Plastic Injection Molding Machine. Established brands often provide more durable and efficient machines. Reliable brands also tend to offer better warranties and support services. Investing in a reputable brand can reduce downtime and maintenance costs.
Customer Support
Customer support is another critical factor. Effective customer support includes technical assistance, spare parts availability, and training. Good customer support ensures smooth operation and quick resolution of any issues. Evaluating the manufacturer’s support services before purchasing can save time and resources.
Evaluating Machine Features
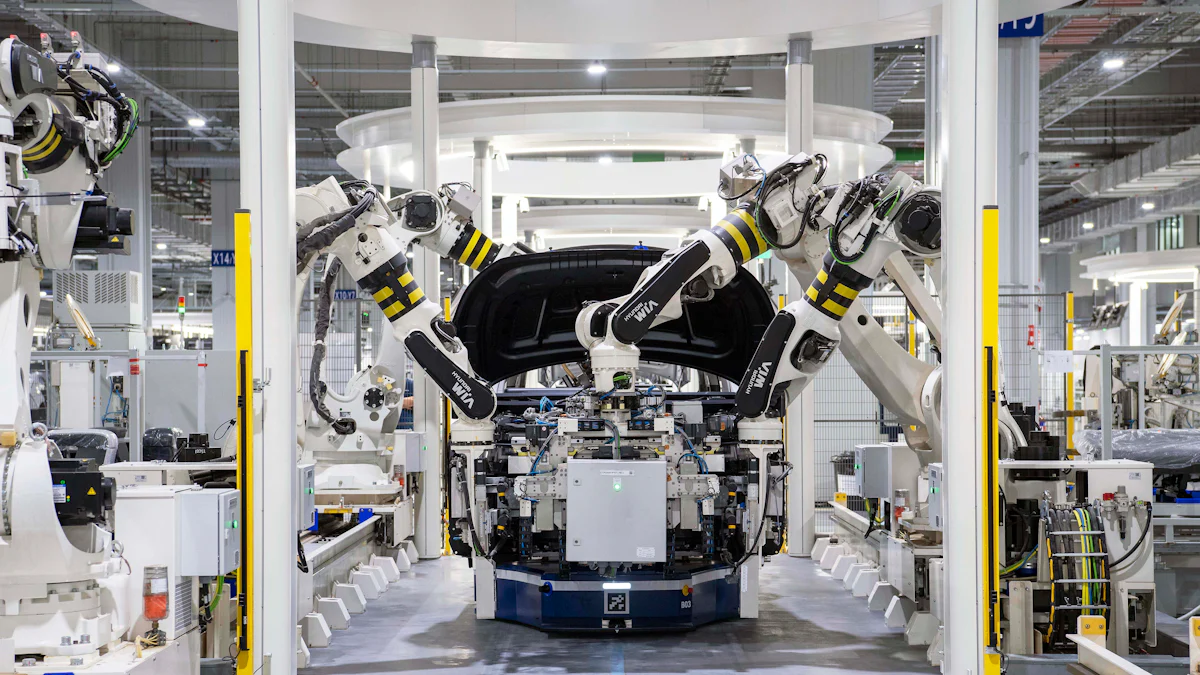
Energy Efficiency
Power Consumption
Energy efficiency plays a crucial role in the overall cost-effectiveness of a Plastic Injection Molding Machine. Modern machines often incorporate advanced technologies to minimize power consumption. Reduced energy usage not only lowers operational costs but also contributes to environmental sustainability. Companies can reinvest the savings obtained from increased energy efficiency into other areas of the business.
Environmental Impact
The environmental impact of a Plastic Injection Molding Machine is another important consideration. Machines with lower energy consumption produce fewer carbon emissions, making them more eco-friendly. Selecting an energy-efficient machine aligns with global efforts to reduce industrial pollution. This choice supports sustainable manufacturing practices and enhances the company’s reputation for environmental responsibility.
Precision and Accuracy
Tolerances
Precision and accuracy are critical in producing high-quality plastic parts. A Plastic Injection Molding Machine must maintain tight tolerances to ensure consistent part dimensions. High-speed injection mold equipment, when appropriately maintained, allows for the mass production of precision-molded plastic parts. Consistent tolerances reduce material waste and improve product quality.
Repeatability
Repeatability refers to the machine’s ability to produce identical parts in successive cycles. Injection molding is known for its high repeatability, making it a preferred manufacturing process. Reliable repeatability ensures that each part meets the required specifications, minimizing defects and rework. This consistency is essential for maintaining product standards and customer satisfaction.
Ease of Maintenance
Availability of Spare Parts
Maintenance is a key factor in the long-term performance of a Plastic Injection Molding Machine. The availability of spare parts significantly impacts machine downtime and operational efficiency. Manufacturers that provide readily available spare parts help ensure quick repairs and minimal production interruptions. This availability is crucial for maintaining continuous operations and meeting production deadlines.
Technical Support
Technical support is vital for resolving issues and optimizing machine performance. Effective technical support includes troubleshooting assistance, regular maintenance services, and operator training. Good technical support ensures that the machine operates at peak efficiency and reduces the likelihood of prolonged downtime. Evaluating the manufacturer’s support services before purchasing can save time and resources in the long run.
Practical Tips for Making the Final Decision
Comparing Quotes
What to Look For
When comparing quotes, focus on several key factors. Examine the machine’s specifications and features. Ensure that the machine meets production needs. Check the warranty terms and conditions. Look for any additional services included in the quote, such as installation or training. Assess the total cost of ownership, not just the initial price.
Negotiation Tips
Effective negotiation can lead to significant savings. Start by gathering multiple quotes from different suppliers. Use these quotes to leverage better deals. Highlight any competing offers during negotiations. Ask for discounts or additional services at no extra cost. Be clear about budget constraints and production requirements. Aim for a win-win situation where both parties benefit.
Visiting Manufacturers or Distributors
What to Ask
During visits to manufacturers or distributors, ask specific questions. Inquire about the machine’s production capabilities. Ask about the energy efficiency and maintenance requirements. Request information on the availability of spare parts. Seek details on the technical support provided. Clarify the terms of the warranty and any after-sales services.
Inspection Checklist
An inspection checklist ensures a thorough evaluation. Check the machine’s build quality and materials used. Inspect the control system for user-friendliness. Verify the machine’s energy consumption levels. Examine the injection and clamping units for any signs of wear or damage. Test the machine’s precision and accuracy by observing a production cycle.
Seeking Expert Advice
Consulting Industry Professionals
Consulting industry professionals provides valuable insights. Reach out to experienced engineers and technicians. Ask for recommendations based on specific production needs. Seek advice on the most reliable brands and models. Discuss potential challenges and solutions. Use their expertise to make an informed decision.
Online Resources
Online resources offer a wealth of information. Visit industry forums and discussion boards. Read reviews and testimonials from other users. Access technical articles and guides on plastic injection molding machines. Watch video tutorials and demonstrations. Use these resources to supplement knowledge and aid in the decision-making process.
Choosing the right plastic injection molding machine involves several key considerations. Evaluating factors such as machine type, specifications, and manufacturer reputation ensures an informed decision. Taking time to compare quotes and seek expert advice can lead to significant savings. Balancing cost and quality remains crucial for long-term success. Investing in a reliable, efficient machine enhances production efficiency and product quality.