Plastic recycling plays a crucial role in addressing the global waste problem. Only 9% of all plastic ever produced has been recycled. The majority of plastic waste, around 72%, ends up in landfills or the environment. Various Plastic Recycling Machine types exist to tackle this issue effectively. These machines range from shredders to pelletizers, each designed for specific functions and materials. Understanding these machines helps optimize recycling processes and promotes environmental sustainability.
Types of Plastic Recycling Machines
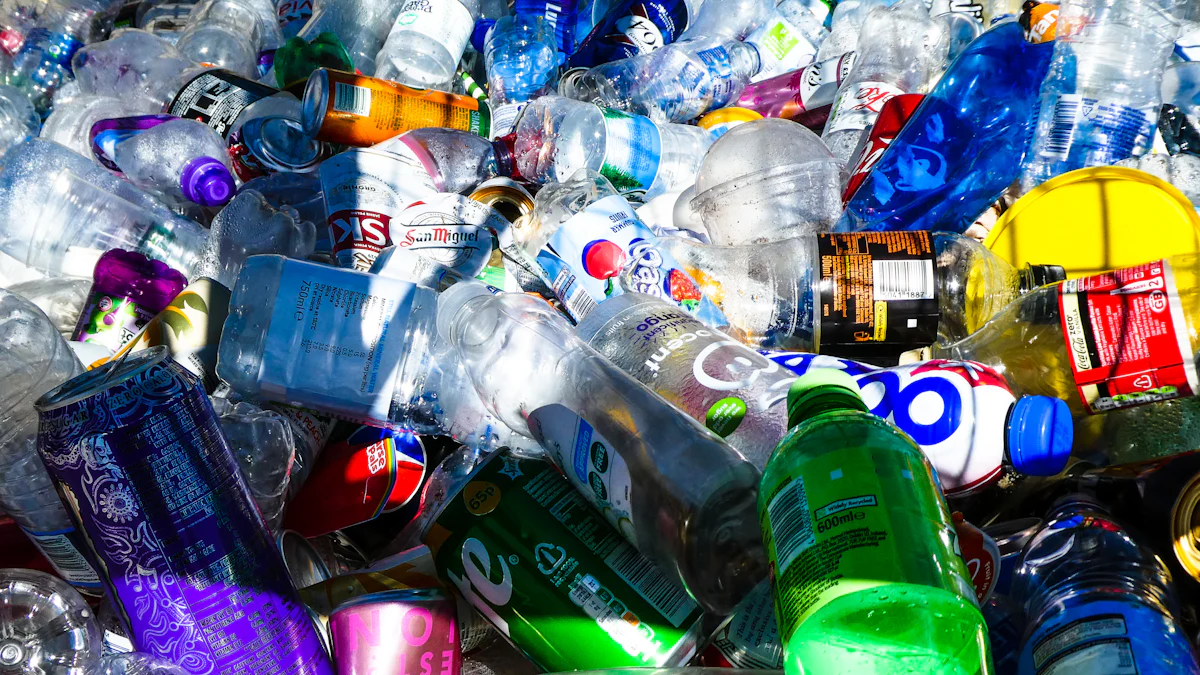
Shredders
Function and Mechanism
Shredders serve as the initial step in the plastic recycling process. These machines break down bulky plastic items into smaller fragments. The shredding mechanism involves rotating blades that cut the plastic into manageable pieces. This size reduction facilitates easier handling, transportation, and subsequent processing.
Types of Shredders
Several types of shredders exist, each designed for specific applications:
- Single-Shaft Shredders: Ideal for light to medium-duty tasks.
- Double-Shaft Shredders: Suitable for heavy-duty operations, providing higher torque.
- Granulators: Often used in conjunction with shredders for finer size reduction.
Advantages of Using Shredders
Using shredders offers numerous benefits:
- Efficiency: Reduces large plastic items into smaller, manageable pieces.
- Versatility: Handles various types of plastic waste.
- Cost-Effectiveness: Lowers transportation and storage costs by reducing volume.
Granulators
Function and Mechanism
Granulators further process the fragments produced by shredders. These machines break down plastic scrap into uniform granules. The granulation process involves rotating knives that cut the plastic into small, consistent pellets.
Types of Granulators
Different types of granulators cater to various needs:
- Central Granulators: Designed for high-volume processing.
- Beside-the-Press Granulators: Suitable for smaller, on-demand tasks.
- Heavy-Duty Granulators: Capable of handling thick and tough plastic materials.
Advantages of Using Granulators
Granulators provide several advantages:
- Uniformity: Produces consistent granules for easier downstream processing.
- Flexibility: Adapts to different plastic types and sizes.
- Reusability: Converts waste into reusable raw materials for new products.
Extruders
Function and Mechanism
Extruders play a crucial role in converting plastic flakes or pellets into new products. The extrusion process involves melting the plastic and forcing it through a die to shape it into desired forms. This method is essential for producing plastic films, pipes, and profiles.
Types of Extruders
Various types of extruders exist to meet different production requirements:
- Single-Screw Extruders: Commonly used for simple extrusion tasks.
- Twin-Screw Extruders: Offers better mixing and compounding capabilities.
- Co-Extruders: Enables the production of multi-layered plastic products.
Advantages of Using Extruders
Extruders offer multiple benefits:
- Versatility: Produces a wide range of plastic products.
- Efficiency: Ensures continuous production with minimal waste.
- Customization: Allows for precise control over product dimensions and properties.
Washers
Function and Mechanism
Washers clean plastic waste before further processing. The washing process removes contaminants like dirt, labels, and adhesives. This cleaning ensures high-quality recycled plastic. Washers use water and mechanical agitation to scrub the plastic. Some washers also use detergents for better cleaning efficiency.
Types of Washers
Different types of washers serve various purposes:
- Friction Washers: Use high-speed spinning to remove contaminants.
- Hot Washers: Employ heated water to dissolve stubborn residues.
- Float-Sink Tanks: Separate plastics based on density differences.
Advantages of Using Washers
Washers offer several benefits:
- Improved Quality: Produces cleaner plastic for recycling.
- Versatility: Handles various types of plastic waste.
- Efficiency: Reduces the need for manual cleaning.
Pelletizers
Function and Mechanism
Pelletizers convert plastic flakes or granules into uniform pellets. These pellets serve as raw material for new plastic products. The pelletizing process involves melting the plastic and extruding it through a die. The extruded plastic is then cut into small, uniform pellets.
Types of Pelletizers
Various types of pelletizers cater to different needs:
- Strand Pelletizers: Produce long strands of plastic that are cut into pellets.
- Underwater Pelletizers: Cool and cut the plastic underwater for smoother pellets.
- Hot Die-Face Pelletizers: Cut the plastic directly at the die face for immediate pellet formation.
Advantages of Using Pelletizers
Pelletizers provide multiple advantages:
- Uniformity: Produces consistent pellets for easier processing.
- Reusability: Converts waste into reusable raw materials.
- Efficiency: Ensures continuous production with minimal waste.
How to Choose the Right Plastic Recycling Machine
Factors to Consider
Type of Plastic Waste
Understanding the type of plastic waste is crucial. Different Plastic Recycling Machines handle various plastic types such as PET, HDPE, PVC, LDPE, PP, PS, and ABS. Each machine has specific capabilities tailored to process certain plastics efficiently. For example, shredders are ideal for breaking down large plastic items, while granulators excel in producing uniform granules from plastic scrap.
Volume of Plastic Waste
The volume of plastic waste determines the scale of the recycling operation. High-volume operations require robust machines like central granulators or heavy-duty shredders. Smaller operations might benefit from beside-the-press granulators or single-shaft shredders. Matching the machine capacity to the waste volume ensures optimal performance and cost-efficiency.
Desired Output Quality
Desired output quality influences the choice of Plastic Recycling Machine. High-quality recycled plastic demands thorough cleaning and precise processing. Washers remove contaminants, ensuring superior recycled materials. Pelletizers convert plastic flakes into uniform pellets, suitable for high-grade plastic products. Selecting machines based on output quality requirements guarantees the production of reusable raw materials.
Cost Considerations
Initial Investment
Initial investment varies significantly among different Plastic Recycling Machines. Basic machines like single-shaft shredders or beside-the-press granulators offer cost-effective solutions for beginners. Advanced machines such as twin-screw extruders or underwater pelletizers require higher initial investments but provide enhanced capabilities and efficiency.
Maintenance Costs
Maintenance costs impact the overall budget of a recycling operation. Machines with complex mechanisms, like co-extruders or hot die-face pelletizers, may incur higher maintenance expenses. Regular upkeep ensures longevity and consistent performance. Choosing machines with lower maintenance requirements can reduce long-term costs.
Operational Costs
Operational costs include energy consumption, labor, and material handling. Energy-efficient machines, such as those designed by Precious Plastic, minimize operational expenses. Plastic Pelletizing Machines with advanced technologies reduce energy usage and improve productivity. Evaluating operational costs helps in selecting cost-effective and sustainable recycling solutions.
Environmental Impact
- Pelletizers: Create uniform pellets.
Informed decision-making ensures efficient recycling operations. Future advancements, such as automation and AI, promise enhanced efficiency and sorting capabilities. Innovations like the UNSW method reduce degradation and costs, highlighting the potential of plastic recycling technology.